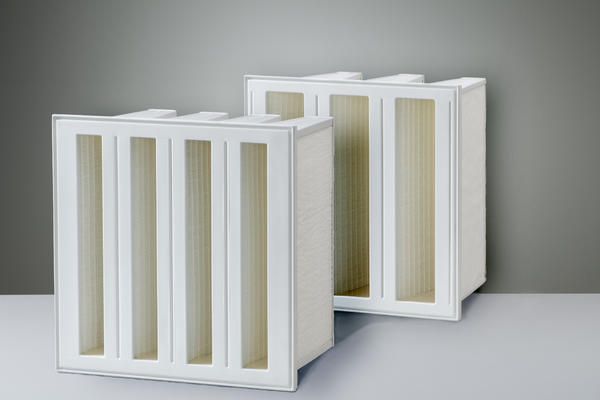
The compressor area is the largest energy consumer in a gas turbine, consuming approximately 60‐
65% of the energy.
1 Even the smallest changes in compressor efficiency have a noticeable impact on
the overall performance of a
gas turbine. According to General Electric, contamination on the
compressor, better known as fouling, is responsible for 70‐85% of the power losses of a
gas turbine.2 The main cause is often inefficient filtration of the supply air. However, the performance deficit can
be sustainably reduced by efficient filtration, as the following field report demonstrates .
2 Cf. J. Janawitz / C. Childs (2015): Heavy-Duty Gas Turbine Operating and Maintenance Considerations.
Stabilization of the compressor efficiency with an EMW® filter upgrade
Site | Coastal region in Northern Europe | |
GT-type | 4x Siemens SGT5-2000E (V94.2) | |
Problem | Steady decrease of compressor efficiency by an average of 2.18% within an observation period of 2 1/2 years despite cleaning of the compressor . | |
Former end filter | Compact filter in filter class F7 | |
EMW® filter-upgrade | (H)EPA compact filter GT in filter class E11 | |
Results | Stable compressor efficiency | |
Effective blade protection without compressor cleaning | ||
Increased availability | ||
Reduced fuel consumption | ||
Increased operating efficiency |
The original filter system was not able to cope with the adverse conditions. The compressor efficiency dropped by an average of 2.18% during the observation period of 2 1/2 years. In the case of heavy particle loading, more severe efficiency losses occurred within a few days. To minimise the efficiency losses in the short term, the gas turbine compressor was cleaned every 2 weeks during operation, but without lasting success. In addition, a thorough offline cleaning of the compressor was carried out every year .
The reduced compressor efficiency had a no ceable effect on the overall performance of the gas turbine. According to a study by Ulf Schirmeister and Frederick Mohr, a 1% decrease in compressor
efficiency is accompanied by a 0.4% decrease in
gas turbine efficiency.3
In this case, the gas turbine's
output level experienced a decrease of up to 2.18%. The main culprit for the output deficit was an
inefficiently acting filter system.
3 Cf. U. Schirmeister / F. Mohr (2016): Impact of enhanced GT air filtration on power output and compressor efficiency degradation.
Gas turbine | SGT5-2000E | |
Nominal power | 187 MW | |
Reduced compressor efficiency | Ø 2,18% | |
Compressor cleaning | 2x online / month | |
1x offline / year |
In order to make a comparison at the site, EMW® installed a filter upgrade of (H)EPA filter class E11 on another gas turbine during the same period. With lasting success for the power plant operation !
(420 filters per filter stage ) | Original filter system |
EMW Filter‐upgrade |
Gas turbine |
GT 1 |
GT 2 |
End filter |
Compact filter GT in F7 |
Compact filter GT in E11 |
Volume flow per filter |
3669 m³/ h |
3669 m³/ h |
The supply air enters the filter house via three inflow sides. 420 air filters are installed per filter stage. The volume flow is approx. 3669 m³/h per filter. Previously, the last filter stage contained a compact filter of filter class F7 according to EN 779. EMW® has implemented an upgrade with a GT compact filter of (H)EPA filter class E11 in a filter house and compared the results of the compressor efficiency in parallel operation.
No changes to the filter house were necessary to implement the filter upgrade!
According to the operator, the initial pressure difference of the end filter stage showed an increase
of only 8 per cent from approx. 120 Pa to 130 Pa. This is because, in comparison, the (H)EPA end filter from EMW® stands out with a filter area that is almost 55 percent higher than the original end
filter in F7. The development of the pressure difference was stable for the EMW® filter system during
the runtime. In the comparison period of 2 ½ years, the pressure difference of the (H)EPA air filter from EMW® increased by 150 Pa. A filter change was not necessary during this period .
End filter of the original filter system |
(H)EPA End filter
EMW® Filter‐upgrade
|
|
Initial pressure difference End filter 3669m³/h | Approx. 120 Pa | Approx. 130 Pa |
Service life | 2 1/2 years | 2 1/2 years |
End pressure difference after 2.5 years |
250 Pa | 280 Pa |
An increase in the pressure difference has a linear effect on the output as well as the fuel
consumption of a gas turbine. A pressure increase reduced by 50 Pascal can result in an increased
output of approx. 0.1% (cf. Wilcox 2010: p. 15). However, various studies indicate that significantly
greater optimisation potentials can be realised through higher efficiency of a filter system or through
higher quality of the contributed air quality. The following results of this study are similar .
As can be seen in the following chart, the collection efficiency of the original compact filter in F7 has
a significantly lower collection efficiency in the particle spectrum <0.3 µm than the (H)EPA compact
filter in E11 from EMW®. It is particularly important to prevent this particle spectrum from entering
the compressor in order to ensure compressor efficiency. Because the goal of the power plant team
and the EMW® team was: to stabilise compressor efficiency!
The significant differences in the separation efficiency of the air filters had a direct impact on the appearance of the respective gas turbine compressor, as the following photographs illustrate.
The significantly cleaner appearance of the compressor had a direct impact on its efficiency. Whereas the compressor efficiency at GT#1 showed losses of 2.18% on average despite continuous cleaning of the compressor, the compressor efficiency losses (isentropic) at GT#2 with the EMW® upgrade remained stable between 0 ‐ 0.11% over 2 ½ years. At the same time, the unit continuously operates at a higher level of compressor efficiency, while the unit with the original fine filter system only achieves a similar efficiency level for a short time and then immediately drops again. No cleaning of the compressor took place over the period on the gas turbine in question, which was equipped with the (H)EPA upgrade from EMW®.
The GT with the original air filter system showed an average power loss of 2.2 MW per operation hour, whereas the GT with the upgraded HEPA E11 filter system showed during the same time only a power loss of approx. 350kW. Due to the continuously optimised compresser efficiency, the fuel consumption was reduceed by approx. 405 kg per operation hour. Accordingly, the CO2 emissions were reduced by approx. 1526 kg, which leaves an environmental footprint.
As a result of the successful upgrade, all gas turbines at the site are now operated with EMW® (H)EPA compact filters.