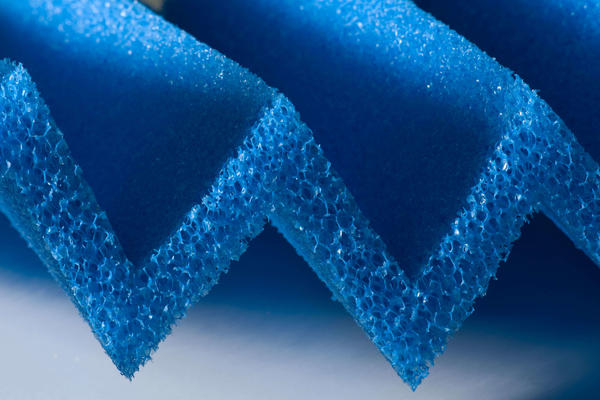
Location | Industrial site in a coastal metropolis of Southeast Asia | |
GT-Type | 2x GE LM6000 | |
Problem | Extremely short service life of the filter system between 3 to 10 months caused unscheduled stops in operation. In addition, an inefficient filter system led to a decline in performance of the gas turbines. | |
Former Filter System | Panel filter of filter class G4 | |
Compact filter in filter class F8 | ||
Editional Equipment | Evaporative cooler located upstream of the filter system. | |
EMW® Filter-Upgrade | Poret® coalescer-medium | |
Pocket filter GT in M6 | ||
Compact filter GT in F9 | ||
(H)EPA compact filter GT in filter class E11 | ||
Results | Extended service life of 24 months instead of the previous only 10 months | |
Lower initial pressure drop than with the OEM filter configuration and reduced pressure drop during operation | ||
More efficient filtration leads to more effective protection of the blades without cleaning the compressor | ||
Increased availability of the gas turbines |
Data sheets from filter manufacturers show various data on the filter efficiency and pressure drop of an air filter. The filter efficiency is recorded for different particle sizes. The pressure drop is given as the initial pressure drop at different air flow rates. In practice, however, this filter mix often differs from the results achieved by an air filter under test conditions.
For example, some operators of gas-fired power plants often struggle with an unstable development of the pressure difference in the area of their supply air filter system. Unscheduled filter changes with associated operation stops of the gas turbine can be the result.
The following project from South-East Asia also showed a corresponding problem. The operator used to follow the theoretical assumption: the more efficient the air filter system, the higher the pressure drop and the shorter the operating time of the air filters. EMW® was able to impressively disprove this calculation.
In this case, two General Electric LM6000 gas turbines are in base load operation. The gas turbines have a rated output of 32 MW each. The local environmental conditions are characterised by an industrial location in a tropical region close to the coast. The annual average temperature is about 26.4°C. The summer dry season is replaced by monsoons with heavy rain in winter.
The original filter system was not able to cope with the adverse environmental conditions. Within a few months, the filter system reached a rapid increase in pressure drop, so that the load of the gas turbine had to be reduced. Depending on the season, the intervals for changing the filter system ranged from 3 to 10 months. Due to the low and unreliable operating time of the filter system, unplanned operational stops were the result. Another shortcoming of the filter system was that it was extremely inefficient at removing particles. As a consequence, the compressors of both gas turbines had to be cleaned continuously in order to limit performance losses.
The supply air enters the filter house via two inflow sides. For each inflow side, 2 filter stages are integrated, which are divided between two filter walls. Initially the set-up was configured with 100 filters per stage. This OEM configuration was upgarded to a system with 124 filters per stage. After this upgarde the system operated in the first filter stage with 124 pre-filters of filter class G4 according to EN 779 followed by 124 final filters of filter class F8 according to EN 779. The load is approx. 4150 m³/h per filter. The service life of the pre-filters and final filters was a maximum of 10 months. Thus, the filter system clearly missed the operator's intended maintenance interval, which was scheduled at 12 months.
The upgrade from EMW® features a much more stable and efficient GT pocket filter variant in filter class M6 according to EN 779 on the first filter wall. On the final filter wall, a compact filter GT of filter class F9 is directly coupled to a (H)EPA compact filter GT of filter class E11. The compact filters in F9 and E11 both achieve a service life of 24 months. This means that the operator's planned maintenance window could be doubled. The pre-filters could achieve a service life of more than 12 months, but are replaced after 12 months during the planned maintenance interval.
For droplet separation, the Poret® Coalescer Media was integrated before the first filter wall. Poret® is washable and reusable. After a wash cycle, the medium looks brand new again and also acts accordingly reliably. The duration of reusability is usually 24 months.
No changes to the filter house were necessary to implement the filter upgrade!
Unit 1 LM 6000 | Unit 2 LM 6000 | ||
---|---|---|---|
Filter stage | Filter per stage | Original filter system | EMW® Filter-Upgrade |
Coalescer | n/a | Poret® coalescer-medium | |
Filter class type Pre-filter | 124x | G4 Panel filter | Pocket filter GT in M6 |
Filter classes second and final filter stage | 124x | Compact filter GT in F8 | GT Compact filter in F9 coupled to GT Compact filter in E11 |
Volume flow per filter | 4150m³/h | 4150m³/h | |
Despite the integration of further filter stages, the EMW® filter system was able to show duirng operation a pressure drop that was reduced by half in comparison to the previous system. In addition, the gas turbine was protected from contamination, so that online and offline cleaning is now obsolete. This increases the availability and performance level of the LM6000 gas turbine. Meanwhile, the EMW® filter concept has been transferred to both LM6000 gas turbines.
The area between the red trend and the blue trend shows the filter performance of the EMW® filter upgrade. Thus, almost the entire incoming particle load at the site is separated by the EMW® filter system and the gas turbine and power plant operation is optimally protected!
The video was taken during maintenance work. Thanks to the EMW filter upgrade, the compressor of the LM6000 gas turbine does not show any contamination, so that no cleaning of the compressor was necessary between the maintenance intervals of 12 months.